What Is Equipment Management | Gecko
Written by Gecko
What Is Equipment Management? Tips To Achieve Quality Results Fast
What is equipment management? It’s the backbone of running a business efficiently and effectively, especially in the rental industry.
Whether you’re managing a party rental business handling back-to-back bookings or an event equipment rental company overseeing a diverse selection, smart equipment management helps save time and avoid costly errors. Maintaining your assets, performing regular maintenance and allocating resources effectively will help you maximise your resources and keep operations running smoothly.
Effective equipment management means leveraging data to its fullest potential, and the right equipment rental software can help with that. Analysing usage patterns can help redistribute underused resources, support equipment sharing across teams and guide decisions on retiring or repurposing outdated gear. Clear procedures and continuous training empower your team to handle equipment with confidence.
Now that you have the answer to ‘What is equipment management?’ here are some tips to achieve quality results quickly:
Tip #1: Use smart tracking systems for your equipment.
Barcodes and QR codes are game-changers for equipment management.
These codes, once attached to your gear, allow quick and efficient scanning for seamless tracking as items are checked in and out. The simplicity of scanning reduces human error and makes inventory checks straightforward and less time-consuming. Adopting this system ensures that records are not just accurate but also easily retrievable, facilitating better operational flow.
GPS monitoring also offers precise tracking of equipment locations.
By utilising GPS technology along with robust rental management software, you can monitor where your assets are in real time, providing peace of mind, especially for high-value items. This capability ensures you know whether your equipment is across town or nearby, reducing the risk of theft or misplacement.
Understanding location data is critical in managing logistics, ensuring efficiency and cutting down unnecessary tracking efforts.
Integrating tracking systems with inventory software illuminates equipment management. This integration allows data from barcode scans and GPS tracking to feed directly into your inventory system, providing a clear view of equipment status.
When you have all this information centralised, you can easily detect patterns, schedule maintenance and make informed decisions regarding equipment utilisation.
Tip #2: Schedule regular maintenance to avoid downtime.
Regular maintenance is crucial for preventing equipment breakdowns.
By establishing a comprehensive maintenance calendar, you ensure all machinery undergoes routine check-ups, reducing the likelihood of unexpected failures. This calendar acts as a preventive measure, allowing you to identify and address potential issues before they escalate into costly problems.
Organising maintenance schedules also assists in managing time effectively, ensuring that these checks do not disrupt your day-to-day operations. Through careful planning and scheduling, equipment remains reliable and operational. An organised maintenance calendar is key to sustaining equipment functionality.
Even when you have reliable party rental software in place, it’s helpful to train your team to spot issues during routine checks. Your team serves as the first line of defence against mechanical issues, detecting potential problems early. Training them to notice early warning signs, such as unusual noises or apparent wear, enables smaller issues to be addressed promptly before they worsen.
Tip #3: Get the most out of your equipment.
Identifying underutilised equipment through usage data can offer substantial benefits.
Often, some equipment sits unused while others are in relentless demand. Analysing these usage patterns helps uncover such inconsistencies, paving the way to optimise resource allocation. With these insights, you can make calculated decisions on whether to redistribute resources or adjust your inventory according to actual needs.
Sharing equipment across departments – the way your team works on one centralised rental industry software – can greatly boost efficiency. Instead of letting valuable tools sit idle in one department, implementing a sharing setup ensures resources are effectively utilised across the board. This strategy keeps operations running smoothly without the need for additional investments.
Retiring or repurposing outdated equipment is also key to resource management. Holding onto obsolete assets drains resources and clutters valuable space.
Conduct regular inventory assessments to identify items that are redundant or have outlived their usefulness. Decisions can then be made to sell, recycle or adapt these resources, freeing up capital and space for more pressing needs, such as upgrading your booking software for rentals to optimise your operations.
Tip #4: Invest in training and support for your team.
Comprehensive training on equipment usage is pivotal for seamless operations.
When all team members understand how to handle equipment correctly, the chance of mishaps significantly decreases. This shared knowledge ensures that events run smoothly without the disruption caused by preventable errors. A unified understanding fosters collaboration, allowing teams to work together efficiently and anticipate each other’s needs.
Having detailed Standard Operating Procedures (SOPs) also enhances consistency.
Imagine a centralised manual that precisely outlines the use of every piece of equipment. This is what SOPs offer, ensuring each team member can refer to the same guidelines, thus reducing misunderstandings and errors. They facilitate smooth onboarding for new team members, cutting down training time and helping them quickly integrate into the workflow.
With a clear framework in place, team members can act confidently, knowing they are adhering to established protocols. SOPs are your toolkit for consistency and efficiency.
Additionally, continuous learning is essential to stay current with technological advancements. As equipment evolves, team familiarity with the latest features and best practices becomes crucial for maintaining operational efficiency. Encouraging ongoing education helps your team harness the full potential of new technologies, securing a competitive edge.
Regular training sessions and workshops ensure that everyone remains agile and capable, preventing obsolescence in skills and knowledge. An adaptive and knowledgeable team is always ready to embrace the future. Keeping your team informed ensures they remain effective and forward-thinking.
Key Points to Remember
- Equipment management is about using smart systems like barcodes, QR codes and GPS tracking to streamline operations and reduce errors.
- Schedule regular maintenance to avoid downtime and ensure your equipment stays reliable while preventing costly breakdowns.
- Maximise equipment use by analysing data to reallocate underutilised resources, share tools across teams and retire outdated gear.
- Invest in team training and clear procedures to ensure safe, efficient equipment handling and maintain consistent operations.
- Stay adaptable with the latest technology to enhance equipment management and keep your business competitive and efficient.
Gecko makes equipment management effortless by streamlining inventory tracking, bookings and maintenance through user-friendly software. With features like real-time updates, automated invoicing and delivery coordination, Gecko helps businesses save time and boost efficiency.
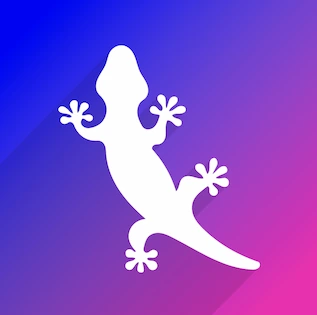